With a growing focus on climate commitment, MedTech companies are examining how their products are repaired, refurbished and recycled. The Health Solutions team at Flex is partnering with them on their sustainability journey to develop and implement tailored circular solutions to prolong a product’s life and shift from a linear take, make and waste approach.
Stefano Vicenzetto, Design Systems Engineer at Flex, has more than 12 years of experience leading the development of medical products as well as Design for Environment expertise. In this column, he shares his insights on how Circular Economy principles can be applied within the Medtech industry, starting with design, to reduce environmental impact.
Within the medtech industry, the term sustainability is well known, but what is meant exactly by Circular Economy?
Vicenzetto: As opposed to the traditional linear economy, where the products are manufactured, used and finally disposed of, the Circular Economy aims to limit the use of raw materials and the production of waste. It does this by recovering and reusing as many materials and products as possible, through the 4R loops: Reuse, Repair, Remanufacturing and Recycling.
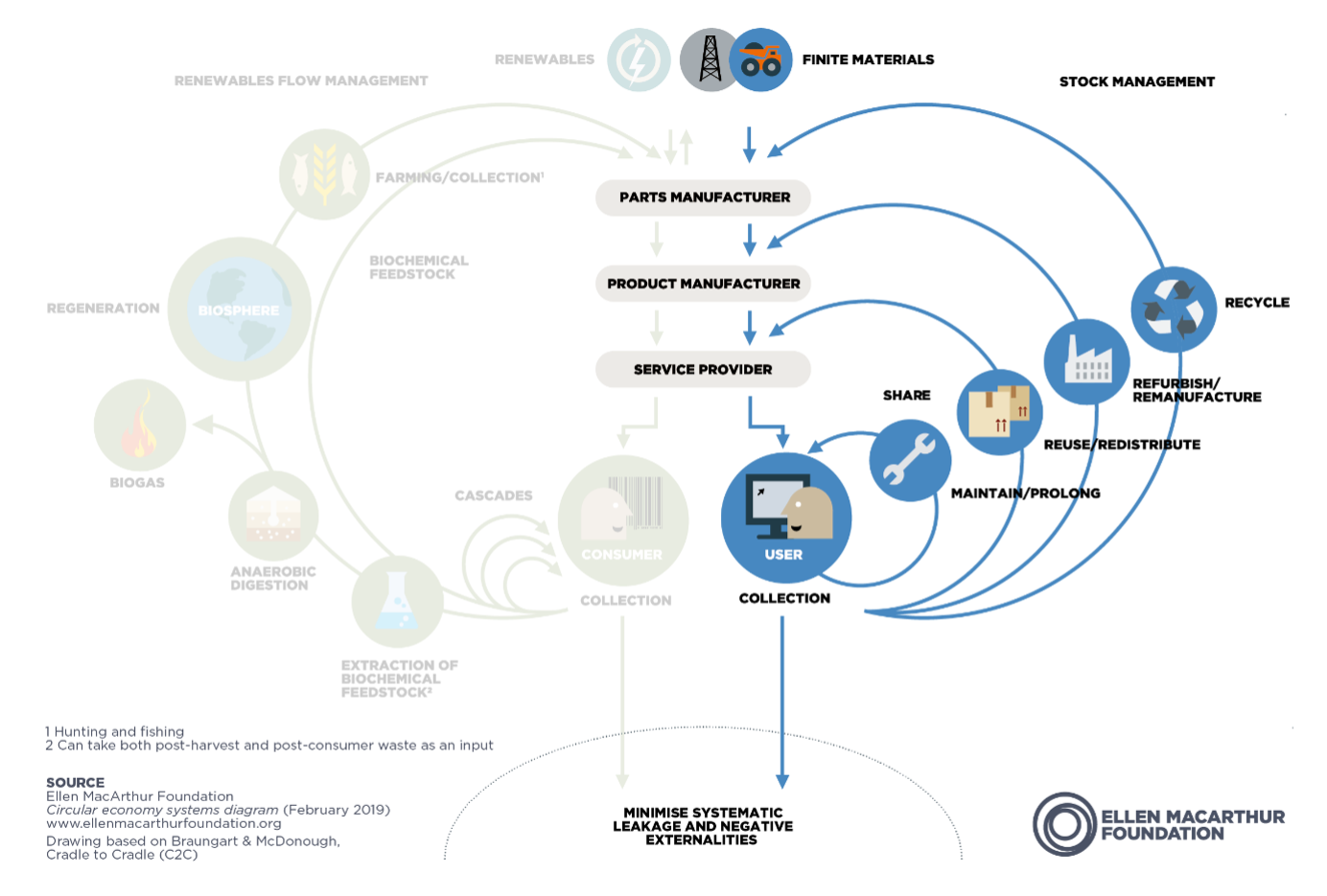
In order to support the 4R loops, a product must be designed according to specific Design for Environment guidelines. In other words, we can say that the Design for Environment is an enabler for the Circular Economy.
When creating new medical products, what are the key aspects of Design for Environment?
Vicenzetto: The Design for Environment guidelines aim to design a product with the following key targets:
- Use sustainable materials
- Extend product durability
- Improve energy efficiency
- Ease disassembly and reassembly
- Ease maintenance and repair
When designing medical products, the challenge is to integrate sustainability into the classic functional needs and constraints, since medical requirements might be in potential conflict with sustainability goals. For example, biocompatibility requirements may inhibit the use of recycled materials, and the opportunity for medical product reuse can be limited if the product is considered a biohazardous waste. Despite these barriers, many Design for Environment guidelines can be applied to medical products.
Can current devices be redesigned to meet sustainability requirements instead of obsoleted, and what are the best tools for doing so?
Vicenzetto: Yes, an in-market product can be redesigned to meet sustainability targets, and Design for Environments principles can also be subsequently applied.
For existing devices, two methodologies are applied: Life Cycle Assessment and Eco Value Analysis.
A Life Cycle Assessment is the evaluation of the environmental impact of a product and its components. The environmental impact can be assessed using different metrics, such as CO2 emission, energy and water consumption, recycling and recovery rate.
With the Eco Value Analysis, the device can be analysed against the five key targets mentioned above, to identify where improvements can be made applying the Design for Environment guidelines.
Each improvement identified can be finally assessed regarding design impact and potential environmental benefits: the medical device manufacturer can decide which improvements to implement in the product redesign, finding the best solution to reach the sustainability targets minimizing the design impact.
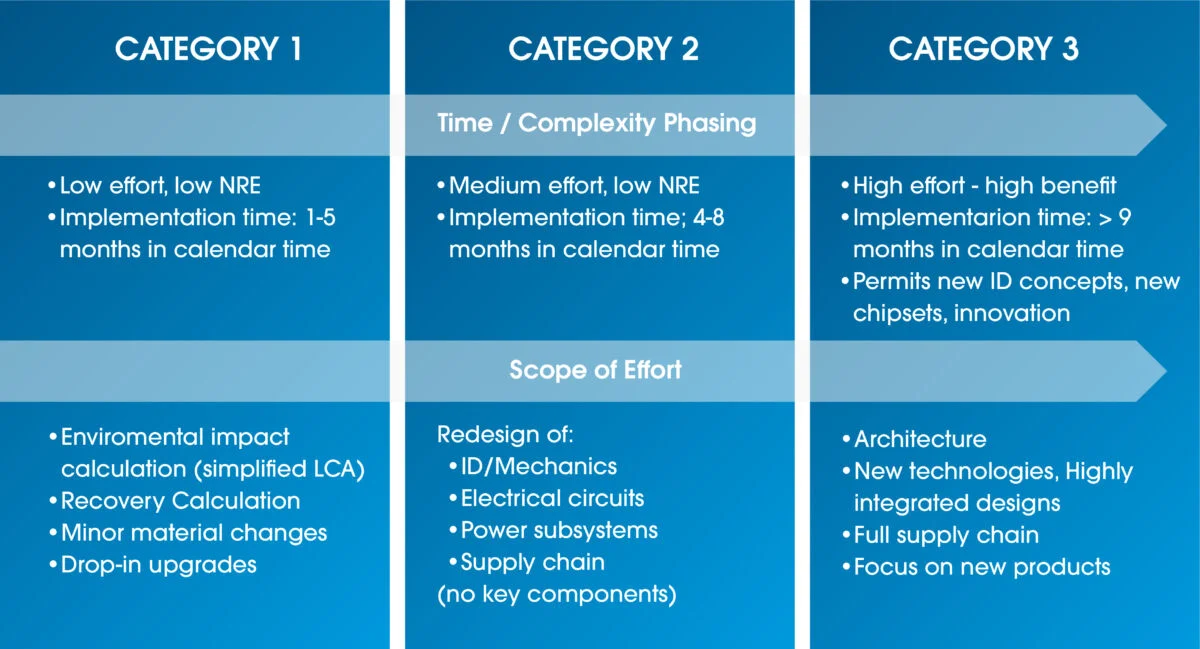
What is an example of a medical product using DfE principles?
Vicenzetto: One example of medical device designed using DfE principles is the Flex Smart Autoinjector reference design platform. The autoinjector was built around DfE guidelines to reduce its environmental footprint and address areas of improvement for product sustainability identified in many drug delivery devices on the market today.
The Smart Autoinjector platform uses numerous eco-smart designs, such as:
- External case made of recyclable plastics to increase the recycling rate
- Long-life rechargeable batteries instead of disposable non-rechargeable ones
- Secure remote upgrades for firmware on the autoinjector platform to extend product durability
- Minimization of product dimension to lower the overall CO2 emissions
- Easy disassembly, to better enable repair, refurbishment, or parts separation for reusing, recycling, or disposal
Download How redesign can help meet sustainability demands for medical devices to learn more.