When a medtech company is audited by the FDA or any other regulatory body, it can be a long and expensive process. Rather than a focus on compliance, the FDA’s Case for Quality Initiative is looking for manufacturers to shift their focus to ensuring quality is built into products and processes rather than inspected out at the end. Modern manufacturing execution systems (MES) can help companies achieve this, remove a lot of the pain associated with audits, and reduce both cost and risk in manufacturing processes.
The shift from focusing on compliance to concentrating on product quality, with compliance simply as a baseline, is important on numerous levels. A reactive approach of tackling problems as they arise makes no sense compared with a proactive approach of preventing the problems in the first place. By taking this approach, production becomes more efficient, costs are lowered, the brand is strengthened, and risks to the business are reduced. For any manufacturer, a product recall is a costly process. To recall an implantable medical device, such as a cardioverter defibrillator, however, could have the added issues of surgical removal and replacement—and the costs could become astronomical!
Measuring Risk
The FDA and other regulatory organizations have both statutory requirements and the authority to audit companies. Although historically based on time periods, the frequency of audits can now be based on risk assessment. For the FDA to be able to operate its audit functions in this way, however, it needs to be able to measure levels of risk. This involves a move to requesting or requiring the industry to provide metrics to show levels of compliance and, more importantly, product quality. When this data is provided, the FDA can evaluate the risk associated with a particular manufacturer, product or production site and adjust its audit schedule accordingly.
If the FDA can evaluate risk and see that processes are in control and in line with quality specifications, this can streamline the audit process and can mean that companies are audited less frequently. The FDA may even choose to audit remotely, avoiding the interruption to normal operations of having FDA inspectors on site. Implementing the right MES solution puts companies in a strong position to achieve this goal.
The Cost of Inspection
FDA inspections are expensive. A targeted inspection has the potential to cost a business hundreds of thousands of dollars in time and resources. Audits or inspections can be triggered by several events. A routine inspection could be part of the FDA work plan. Pre-approval inspections occur when new products are submitted to the FDA for clearance. A 30-day notice audit could be the result of a process change. If the FDA identifies a trend in areas such as adverse event reports or field issues associated with a product, these too could trigger an inspection. The way to avoid increased inspection frequency is not to have quality issues in the first place.
As part of research by Axendia, an analyst and strategic advisory firm for the life sciences industry, 54% of product recalls were associated with manufacturing quality-related issues. The implementation of an MES could have prevented these problems—representing a huge return on investment.
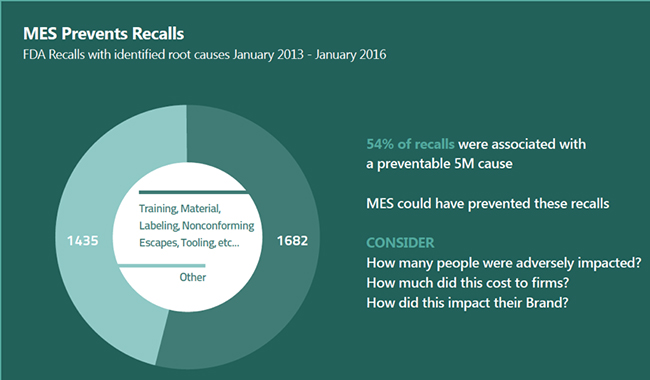
Modern MES not only offers a way of reducing audits through improved quality, they also provide a pathway to efficiently dealing with audits when they arise. If the FDA come to a site and demands documented evidence that specific manufacturing processes are in control, the traditional paper-based systems for storing data make it difficult to quickly provide the required information. Indeed, if the required evidence is from a historical batch, the documentation may well be stored offsite and it could days to retrieve. The more time the inspector must spend at the facility, the more information may be requested, increasing workload for staff supporting the audit. An electronic system, however, can provide information almost instantaneously and dramatically reduce the amount of time that an inspector is on site. As well as quickly demonstrating processes are in or back under control, such a system further gives the regulatory body a level of comfort that they will remain this way.
Prevention Is Better than a Cure
An age-old saying in matters of healthcare, “prevention is better than cure” rings true for medtech manufacturing processes. In Axendia research, 85% of medical industry practitioners questioned said the role of quality was compliance. Only 10% stated that their role was process or product improvement.
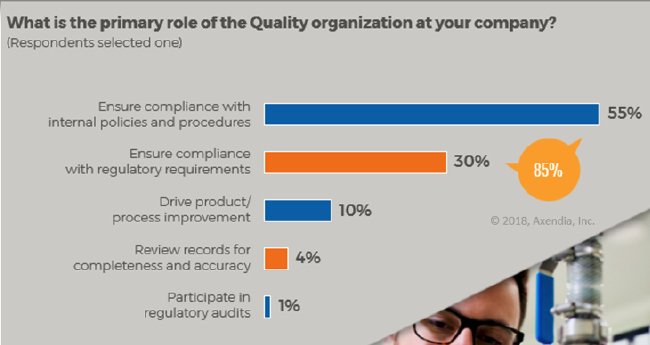
By digitizing processes, any processing issues are dealt with contemporaneously, as opposed to adding detail to paper after they happen. Nearly 80% of FDA notice of violations (Form 483 observation) are not because of a fault in the process or procedure, but because of human error in not following procedure or erroneous manual data entry. The MES controls processes and enforces procedures to stop this from occurring and data is automatically logged with complete traceability throughout the production line, and even into the supply chain. As measurements are collected, the MES can also instantly adjust processes or flag the issue to prevent the opportunity for error and, therefore, reduce opportunity for inspection or audit.
“Building quality into the product saves money. By producing a two or three sigma product, compliance becomes 20–30% of the cost. Improving quality to a six-sigma product reduces this to 2–3%—and this goes straight to the business’ bottom line. Furthermore, are patients not surely entitled to six-sigma quality products?” said Daniel R. Matlis, president of Axendia.
The huge costs associated with product recalls are also lost opportunities for investment in research and development, manufacturing and automation Without the need to react to process errors and quality issues, personnel can move into proactive roles to further improve quality and production efficiency.
Global Businesses Have a Bigger Audit Headache
Although there is some harmonizing and a memorandum of understanding between some regulatory authorities to accept each other’s audits, this is by no means all of them. Global companies could therefore face audit or inspection from numerous health authorities, which could exponentially increase the time and costs associated with compliance. Not inviting this scenario by avoiding quality issues becomes an even more appealing business outcome.
MES Helps Build Quality
Ultimately, any opportunity for error is an opportunity for audit or inspection, and this is a huge disruptor to normal operations. By having a system that supports well designed and executed manufacturing and quality processes, compliance becomes a benign side effect of the resulting quality. Documented evidence for inspectors becomes part of the process, rather than an extra step. A fully automated MES also works proactively to prevent problems with real-time data, business control and advanced analytical capability without risk of human error.
Using an MES to build quality into a medical device therefore reduces the frequency of audits and the risk of product recalls. Even at the most basic level, having documentation and information about processes quickly available wherever and whenever needed reduces the man hours needed to prepare for an audit.
It shows processes are under control, gives authorities confidence that this is the case and decreases the amount of opportunities for a business to receive ‘483s’ or other written warnings.
The FDA’s Case for Quality Initiative is a sound principal and for businesses that fully embrace an ethos of building in quality rather than compliance, there are many benefits to be gained. Having a good standing with the FDA could mean it considers waiving pre-approval inspections if appropriate and, even if a product recall is necessary, the FDA is more likely to talk through issues and work with the company rather than taking more severe avenues in the first instance.
Of course, the benefits of a modern, future-ready MES go far beyond helping to deal efficiently with regulatory requirements. There are advantages to be gained in production efficiency, facilitation of innovation and faster new product introduction. For the medtech industry, however, the costs to be saved in audit overheads alone make the right MES a sound business investment for the future of a company.