Automation and digitization of quality processes are becoming integral to advanced manufacturing operations. Medical manufacturers are using it more often to improve efficiency, reduce costs, and enhance product quality. MTI recently discussed how this digital transformation is improving MedTech manufacturing quality with Garth Conrad, VP Vice President – Quality, Flex Health Solutions.
MTI: Can you explain how digital quality differs from traditional quality management practices?
Conrad: Traditional quality practices in the Medical Device industry rely on paper-based artifacts to demonstrate process compliance. These records serve as evidence of adherence to quality standards. In contrast, digital quality management practices leverage data-driven approaches, where records are not physical artifacts, but digital information collected from systems used to manage and control processes. This shift towards digital quality allows for more efficient and accurate data collection, analysis, and interpretation, leading to improved quality management and compliance within the industry.
MTI: Can you provide examples of how automation and digitization of quality processes have improved manufacturing outcomes?
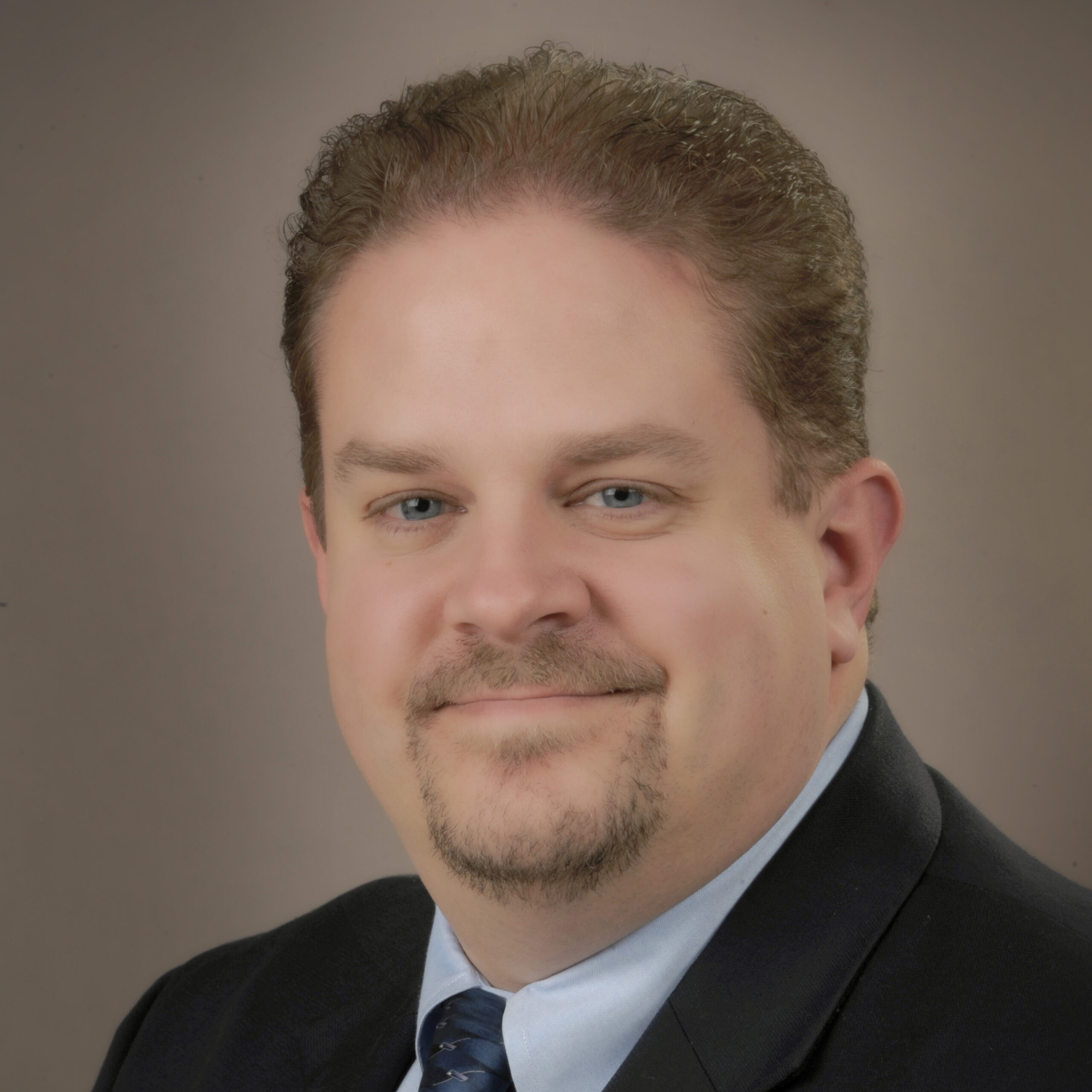
Conrad: Automation and digitization of quality processes have revolutionized manufacturing outcomes in several ways. Real-time monitoring using automated sensors and data collection systems allows manufacturers to detect deviations and take immediate corrective actions, preventing defects and ensuring consistent product quality. Automated inspection technologies like machine vision systems enable faster and more accurate inspections, reducing human error and improving quality control. Predictive analytics algorithms analyze historical and real-time data to identify patterns and trends, helping manufacturers anticipate quality issues and optimize production processes. Digital documentation and traceability streamline audits, reduce paperwork, and enhance compliance with regulatory requirements.
By digitizing quality processes, manufacturers can create and manage digital documentation, making it easily accessible and trackable throughout the manufacturing process. This simplifies collaboration among stakeholders, allowing teams to share real-time quality data, collaborate on problem-solving, and communicate effectively to address quality issues promptly. This collaborative approach improves communication, decision-making, and overall quality outcomes. Overall, automation and digitization of quality processes have led to improved efficiency, reduced costs, and enhanced product quality in manufacturing.
MTI: What are some common challenges manufacturers face when adopting digital quality, and how can they overcome them?
Conrad: Resistance to change is a common challenge when introducing new technologies, especially if employees don’t fully understand them. To overcome this, organizations can implement a Change Management Plan and communicate frequently with the workforce to improve adoption.
Another important skillset for the workforce is technology proficiency. Employees need to have a solid understanding of the digital tools and technologies being implemented. Providing opportunities for learning, such as self-paced activities or formal classroom-based sessions, can help drive better understanding throughout the organization.
Data management is another critical aspect of implementing digital quality processes. With the increased use of digital technologies, there is a significant amount of data generated. It is essential to store this data securely while also making it accessible for analysis and gaining insights into process performance. Having employees skilled in cloud storage, cybersecurity, and data analysis is key to the success of the digital quality journey.
MTI: What strategies can manufacturers use to ensure smooth integration of digital quality with existing systems and technologies?
Conrad:
- Define clear objectives and realistic goals: Clearly define the objectives and goals of the integration. This will help align efforts and ensure that everyone understands the purpose and expected outcomes. Setting realistic goals will provide a clear direction for the integration process.
- Develop a roadmap and implementation plan: Create a phased implementation plan that builds upon the success of prior stage digital transitions. This will ensure a solid foundation for future processes. By breaking down the integration into manageable stages, you can implement changes gradually and minimize disruptions.
- Engage stakeholders and communicate effectively: Involve key stakeholders from different departments and levels of the organization in the integration process. This includes IT teams, quality assurance personnel, operations managers, and other relevant stakeholders. Effective communication is crucial to address concerns, manage expectations, and ensure a smooth transition.
MTI: What advice would you give to manufacturers who are considering embracing digital quality for long-term success?
Conrad: It is important for manufacturers to approach the adoption of digital technologies with a balanced perspective. As example, while AI has the potential to be a game changer in the industry, it is crucial to recognize that it is not a one-size-fits-all solution for all problems. When considering the implementation of digital technologies, it is essential to ensure that they align with the business objectives and your vision of the future. It is advisable not to be swayed solely by the hype surrounding certain technologies, but rather to carefully evaluate their relevance and suitability for the organization’s specific needs. By maintaining a focused and purpose-driven approach, manufacturers can make informed decisions that will contribute to their long-term success.
Ask the Expert is a sponsored content program. MedTech Intelligence writers and editors were not involved in the creation of this content. Publishing of this content by MedTech Intelligence is not an endorsement of the content, products or services mentioned herein.
This post is sponsored by:
For more information on digital quality in medical manufacturing visit: Optimizing electronics manufacturing with AI and ML