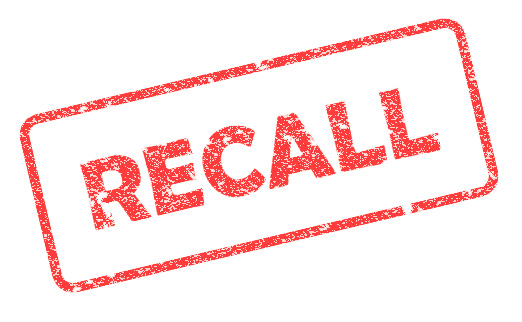
Q3 Medical Device Recalls Fall Nearly 30%, but Still on Track to Exceed 2019
Top reasons for recalls include software, quality and parts issues.
Top reasons for recalls include software, quality and parts issues.
Moving too quickly in the product development process can lead to mistakes.
With digitalization impacting all areas of manufacturing operations, it should come as no surprise that medical device producers must adapt or risk missing the next wave of performance and product improvements.
Across Asia, government health and safety authorities have tightened regulations on medical devices this year, as markets continue to experience rapid change, and as the devices themselves gain sophistication and complexity at a blistering pace.
In general, the Asian markets have controlled the COVID-19 virus successfully outside of China, but its effect has still led to new developments and trends.
Investments in new processes and systems must satisfy the needs of the authorities and ensure patient safety and public confidence. Getting it right is likely to be expensive. but regulatory compliance shouldn’t be viewed purely as a cost center.
As COVID-19 sweeps the globe, it’s becoming increasingly difficult for medical device leaders to navigate the arising challenges and prepare for the future.
The manufacturers failed to comply with requirements related to post approval studies and good manufacturing requirements, respectively.
Smart process automation promises to cut complexity and transform product traceability in the medical device industry. However, its potential relies 100% cent on having good, reliable data on which to draw.
The most successful medical device companies have the same characteristic in common: They’re cross-functional. Whether it be the device design and development activities or quality and regulatory affairs, every operation works together to produce and market medical devices that improve patients’ lives.