For manufacturers of Class II medical devices, the deadline for compliance with the unique device identification (DI) rule is less than six months away. There seem to be varying levels of understanding regarding the rule, which might be why FDA recently released education modules to assist companies.
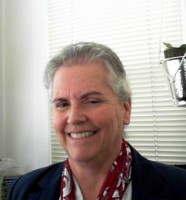
“The biggest issue I’ve seen is that many companies have thought it’s just a labeling issue and so [they say], we’ll give it to our labeling department,” says Linda Chatwin, head of the North American Advisory Services Group at UL. “It’s much more than that, and it touches many areas and resources within a company. FDA tells us that almost half of devices out there are Class II devices, so it’s a huge group that has to go into [the system in] the next few months.” Chatwin adds that while some companies may have the clear understanding of the UDI compliance requirements, they might not have adequate in-house resources to address all the tasks under the rule. Chatwin sat down with MedTech Intelligence to explain how medical device manufacturers can better prepare for the UDI deadline.
MedTech Intelligence: You mentioned that some device companies simply don’t have enough resources to tackle the UDI rule. What resources are required?
Linda Chatwin: Compliance with UDI involves a three-pronged approach:
- Project planning: There needs to be well thought out project plan that includes analyzing product offerings that the company has and gathering certain information about each product. It has to have marketing authorization from FDA, the product code, and listing numbers, and then you have to determine (for each product) all the production information that you attach for each product. Once you gather that information together, you must use one of the issuing agencies that FDA authorizes. Then you have to design the barcode that will go on the product [ensuring that it] provides the appropriate information.
- Process: Take a look at existing processes within the organization and determine what type of labeling, printing, acquisition and suppliers, and what kind of controls on labeling will be required; what printing or labeling mechanisms are being used in manufacturing lines now and do they need updates or changes, etc.
- Reporting into the GUIDID [Global UDI Database] itself: Determining the information that has to be downloaded into GUIDID. Will it be done one record at a time? Should the FDA web interface [be involved]? Will it be done by a third-party submitter in an electronic format or is the company developing the electronic format in house? If they do [it in house], they’ll have a lot of verification and validation work. There’s a lot of be done across the organization, involving regulatory, quality, manufacturing, operations, and the IT department, and management needs to give a firm support to the projects.
MTI: In general, do medical device companies have a firm understanding of the UDI requirements?
Chatwin: I’m guessing that larger organizations have a pretty clear understanding. I don’t think the smaller organizations that manufacture Class II medical devices have enough time and resources, or a clear understanding across the board. I know international companies don’t—I’ve dealt with quite a few that are just completely lost about the requirements.
MTI: FDA recently announced the education modules to help companies understand the UDI rule and prepare for compliance. Any thoughts on the modules? What other forms of education is industry providing in this area?
Chatwin: I’ve seen the modules FDA released, and they’re very good for overview. But they really can’t address the individual questions that companies have for their specific product offerings. Every client I’ve worked with has quite a few special circumstances.
We’ve [UL] provided a number of public webinars, and there are other companies that do the same. But the same issue [comes up]. You’re dealing more on a higher-level general category than what some companies need for their specific situations. I’ve done some private training within companies to help them apply the requirements to their specific circumstances. In other cases, we’ve contracted with companies to go into their facilities and help them get their project plan to a point that it can be implemented and carried out, and then we help the various departments get their procedures in place.
There are always products that are pretty standardized in the way they’re marketed or their intended use. But medical devices have evolved a lot technologically in the last few years. There are a number of them that have special configurations or ways they put add-ons to equipment, so there are so many questions.
MTI: Can you provide some specific examples of the unique/custom needs that device companies have?
Chatwin: I’ve worked with clients that provide a number of disposable products. Some disposable products are reused four to six times, and so the question always comes up: What are my requirements under UDI for direct marketing of these [products], because they’re disposable but we know the doctors reuse them a few times before they really dispose of them?
There are certain products, such as wheelchairs, that have a number of options and are designed to assist patients that have differing types of medical problems. So while there may only be five or six base models of wheelchairs, companies have all these models with different options and more than 200 configurations. How do you handle the UDI on those different configurations? Those issues have to be taken into account, and [you have to] look at whether the accessories are part of a main 510(k) [submission] or a PMA product, or are they really just a component that wouldn’t need a 510(k).
MTI: Regarding Class II devices and the compliance date: What recommendations do you have for device manufacturers that don’t know how to approach the rule?
Chatwin: If they haven’t given some thought as to how to approach it, they should contact someone in the education or consulting business to help them get a kick start, or they’ll be behind the eight ball very quickly. There are so many products that will be downloaded into the GUIDID over the next few months that it’s going to be a clog in the system. If everyone doesn’t have their product entered by September 24, they have a problem. Get some outside help with the knowledge and expertise to help drive you through the process.
Don’t wait. If you haven’t given thoughts to what will be needed to comply with UDI, it’s a complicated area. People may read the regulation and say ‘we can do this’, but there’s a lot to take into account. I recommend getting started very quickly.