Most device designers are well aware of the importance of human factors during product development. As more products allow users to manage information, whether it’s a clinician sharing data from device to device within a hospital, or a patient tracking compliance with a therapeutic routine, there is a higher expectation for user interface quality and interoperability.
“When considering human factors more holistically, you have to think not just about a device working alone, but also how it fits within a system that includes other devices, and whether the various devices have good interoperability,” says Michael Wiklund, general manager, UL-Wiklund (UL’s human factors engineering group). “A device has to play well with others.”
In a Q&A with MedTech Intelligence, Wiklund discusses how manufacturers should be approaching human factors from an investment, product development, and application standpoint.
MedTech Intelligence: What challenges do manufacturers face related to assessing the user experience and identifying risks associated with product design?
Michael Wiklund: Best practice suggests applying human factors from the start of a development effort. If developers do not do this, and perhaps have not even conducted preliminary usability tests of the product, they are likely to have problems validating the device’s use-safety. They’ll likely discover design shortcomings that could have been caught much earlier in the development process or avoided all together. Often, developers perform back-filling activities to ensure a complete design history file, but they’re doing the work, such as conducting user research to write user interface requirements and performing a use-related risk analysis, when the product is nearly finished. This timing limits opportunities for the human factors engineering work to positively influence the final design.
During a validation usability test aligned with FDA’s expectations, people perform critical tasks with a given device. The tasks are those that could lead to harm if the user makes mistakes, but presumably are unlikely to occur due to risk control measures. Mistakes signal user interface design flaws that might have been detected earlier in the development process through preliminary testing.
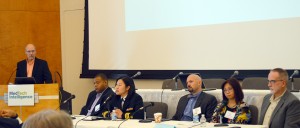
MTI: Why should manufacturers consider human factors an investment rather than a cost?
Wiklund: Companies should be thinking about human factors as an investment, just as they think of investing in any other qualities, such as reliability. Of course, they need to meet the regulatory minimums. Beyond that, they are justified in thinking about how an extra investment in human factors might pay off, just as an investment in industrial design might pay off. When you invest in human factors, you have a right to expect that your devices will deliver a good user experience.
Manufacturers should be making investments in human factors for regulatory and commercial reasons, and they should expect significant ROI. Accruing benefits might include greater sales volume because people find the product intuitive to use; fewer calls to customer support because people are not struggling to use it; simpler user documentation because the device’s use is simpler to explain; and reduce product liability exposure because the device is demonstrably less prone to potentially harmful use errors.
If you produce a device with a great user interface, you might be able to sell it for many more years, rather than being forced to replace it after a few years because a competitor has introduced a more user-friendly device.
MTI: What application areas are ahead of the curve?
Wiklund: I consider many of today’s minimally invasive surgical instruments to be exquisitely well designed. Many of them are wonderful examples of ergonomic design.
I also admire many of what I will call hybrid devices that have both hardware and software user interface elements. For example, there are some dialysis machines, patient monitors, defibrillators, and other equally complex medical devices that are easy to learn and use in a safe and effective manner, largely due to an investment in human factors engineering.
MTI: Home healthcare is growing. Do you see an evolution in how human factors will play into this space?
Wiklund: Devices we normally think of being used by nurses and other healthcare providers are now used by laypersons at home; perhaps the parent of a young child or one elderly spouse helping another. Increasingly complex medical devices are moving into the home partly to reduce the cost of healthcare, to keep people out of hospitals where we know they can contract infections, and to give people more control over their own healthcare. For example, my team was involved in the development of a hemodialysis machine that laypeople will use at home, thereby saving a lot of commuting time and potentially improving their health through more frequent but shorter treatments.