Most medical device implants are designed for mass manufacturing, and are produced in a limited range of sizes and shapes. Surgeons choose a specific implant for a patient, and then surgically fit the patient to the implant. This traditional approach supports standard-off-the-shelf design and manufacture of implants and associated surgical instrumentation, but it isn’t well suited to accommodate personalized devices which require design and manufacturing at a mass customization scale.
As demand for personalized treatments grows, medical device manufacturers are using integrated design, manufacturing and data management software technology to create patient-specific implants and/or surgical instrumentation. Image to implant process automation is a product lifecycle management (PLM) software solution framework that enables implant manufacturers to provide customized products and therapies, automating key steps in an engineer-to-order process to meet speed and accuracy requirements for personalized therapies.
The solution allows manufacturers to securely manage a patient case and its unique design and manufacturing data from initial order to shipment of the personalized implants and/or instruments to the operating room. The system also facilitates the creation and control of required regulatory compliance records, such as the Design History File (DHF) and Device Master Record (DMR).
Collaboration and Automation
During the engineer-to-order design process, the surgeon works with the manufacturer to collaborate on personalized characteristics, and incorporate individual preferences of the surgeon. The collaboration is facilitated via a secure website.
An early step of the image to implant process involves analyzing and transforming a 3D scan of the patient’s anatomy, usually a CT or MR scan, into a highly accurate, digital
3D volumetric models of the anatomy of interest. The 3D volumetric models are then used to define the surgical plan and design the personalized components. The surgeon and manufacturer’s sales representative access the cases online and participate in reviews. Upon surgeon approval, the personalized components are then manufactured to according to the precise specifications for an individual patient.
Computer-aided design (CAD) software plays an important role in automating the patient-specific design process. Design workflows, defined by the manufacturer’s proprietary algorithms for surgical procedure and implant sizing, make use of anatomical landmarks and biomechanical axes that are identified on the 3D volumetric models. CAD software can automate many steps in the design workflow through the use of programmed scripts and templates, making the 3D alignment, sizing, and patient-specific shaping of implants and surgical instruments a fast, accurate and highly repeatable process.
Customization Requires Advanced and Integrated Programming Capabilities
Manufacturing for personalized implants, typically made from casting and subsequent machining of titanium or stainless steel, requires the precision and advanced capabilities in computer numerical control (CNC) programming. Manufacturing of personalized instruments, typically constructed from plastics, can leverage additive manufacturing methods, using 3D printing technology.
Computer-aided manufacturing (CAM) software can help manufacturers accurately produce the complex organic shapes associated with personalized implants or instruments. For example, when precisely machining titanium and stainless steel at high speeds, CAM technology combines advanced tool path strategies with proven machining parameters for high performance.
To streamline the engineer-to-order process, machine programming can be automated. Process templates automatically apply predefined programming methods, setups, operations and tool selections to individual patient cases. After receiving the surgeon approval, the CAM software automatically updates the shape definitions of the surgical instruments and implant referenced by the process templates.
Digital, simulated, program verification saves time on the shop floor with less need for program checking at the machine, contributing to fewer errors that can waste time and costly materials. Manufacturing simulation technologies are applied to provide a complete check of manufacturing and quality inspection data inside the programming system.
In order to optimize productivity, it is important to connect individual software applications (e.g., CAD, CAM, quality systems) within the managed PLM environment. This managed environment for design, manufacturing, and quality planning should also be connected to shop floor Manufacturing Execution Systems (MES) that synchronize planning and drive production. Having an integrated system helps safeguard against significant errors, reduces waste, saves time, and facilitates improved and electronic traceability for regulatory compliance.
To ensure orders are efficiently and correctly manufactured, a distributed numerical control (DNC) solution delivers the program files from the PLM system directly into the manufacturing equipment. This gives production staff access to approved and released programs, setup sheets, tool lists, drawings, 3D models and other data in the managed environment. A direct connection to the centralized PLM database avoids data duplication and manages revisions to make sure the correct manufacturing data is used on the shop floor.
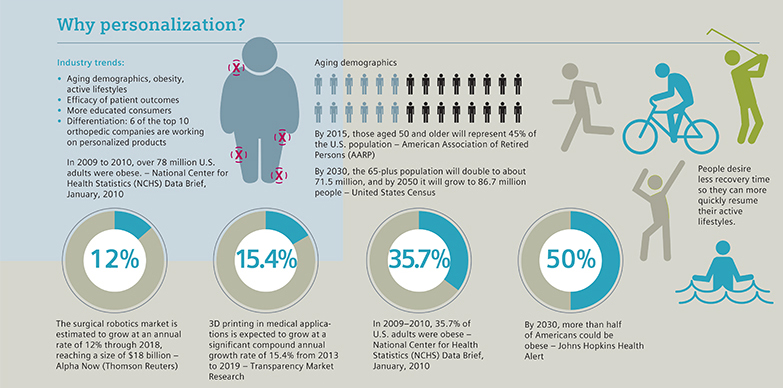
Regulatory Compliance
PLM and MES are essential tools for tracking, monitoring and complying with regulatory requirements. If device companies do not approach compliance from a holistic perspective, there is risk of unbalanced effort expended on mitigation of non-compliance, instead of on building quality into design and manufacturing plans.
Using PLM and MES can help enables companies to maintain and manage their product and process knowledge in a globally accessible system, capturing audit trails, maintaining electronic signatures and facilitating immediate information retrieval.
Conclusion
Beginning with an MR or CT image of patient anatomy and ending with a personalized medical device, companies can automate the entire engineer-to-order process chain for planning, design and manufacture of patient-specific medical devices. Combining a comprehensive PLM system with state-of-the-art CAD/CAM software into an image to implant process automation solution can help device companies economically develop high-quality personalized products while maintaining full compliance with regulatory requirements.