Quality systems at medical device and diagnostic companies are based on well documented standard operating procedures (SOPs) that are efficiently communicated to employees. Introducing SOPs and ensuring that they are followed directly contributes to product and service quality and the overall success of an organization. SOP management includes creating, updating and disseminating information about mission-critical processes, and is often tied to compliance requirements and ongoing quality assurance activities. One could over-simplify this concept by saying that quality systems are all about documenting your current processes and making sure that the stakeholders are aware of and follow them.
Medical device and diagnostic companies, as well as military organizations, manufacturing firms, healthcare providers, and enterprises in many other industries face the day-to-day challenges of SOP management. Confirming that existing processes are compliant with regulations and proving that policies have been followed is challenging enough, but what about managing this process when things change?
Deviations and CAPAs
Deviations inevitably occur, and the results can range from undetectable to catastrophic. For example, a fabrication machine on the factory floor may have been calibrated incorrectly. As a result, product quality is compromised. An investigation uncovers the calibration problem, and ultimately highlights the need for a change to the calibration instructions and the calibration sign-off process.
When any significant deviation is discovered, a related corrective and preventative action (CAPA) must be defined, documented and communicated by the quality management team. The CAPA must then be tracked to verify that the impacted individuals have read and understand the new SOPs associated with the CAPA.
Successful SOP management, therefore, links deviations and non-conformances to related processes and ensures that the SOPs have been read and understood by the appropriate people. Efficient quality systems also try to minimize deviations by encouraging proactive risk management to detect potential problem areas before accidents and deviations occur.
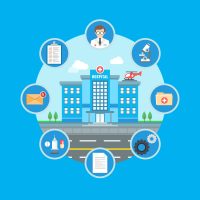
Streamlining SOP Management with EIM
Leveraging an enterprise information management (EIM) system for managing the creation, modification and management of SOP documentation makes sense, as these systems typically offer robust access control management and version control features. However, modern EIM systems help organizations to add value far beyond storing SOP documents:
- Training management. Training on new procedures can be administered via an EIM solution based on employees’ roles in the organization by using workflows and task assignments. Employees “sign off” on their learning requirements with FDA 21 CFR Part 11 compliant electronic signatures, which provide evidence and verification of completed tasks. Role-based assignments also ensure that new employees are assigned relevant learning requirements automatically.
- Change management. An EIM system can help specify a controlled change process for SOPs. Tasks for learning requirements are automatically re-sent to employees if the process has significantly changed, and employees can easily see the highlighted changes compared to the previous version.
- Collecting evidence. Proving to auditors that the organization is following the processes outlined in SOPs can be tricky. EIM systems record the completion of recurring tasks, which serves as evidence during the audit process. If an SOP says that a diagnostic instrument must be checked every day, you can assign this task to appropriate employees who can then verify completion of this task with an electronic signature.
- Streamlining processes. EIM systems help replace paper and Excel-based checklists with electronic forms that leverage electronic and/or digital signatures. The same applies to all approval processes—instead of chasing down people in the office for ink signatures, mobile apps and digital signatures can be used to dramatically streamline approval and task management processes.
SOP management can place a significant burden on quality teams, but best-in-class EIM solutions can alleviate this burden and help teams operate more productively. By aligning EIM and SOP management, organizations can achieve improved transparency, auditing, archiving, security, collaboration and process management.