MHLW MO 169 – Chapter 2/Section 6 – Corrective Action

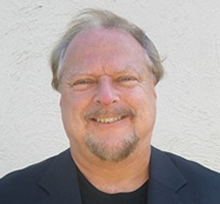
Ohayou Gozaimasu. This week the term/phrase specific to Japan, the doctor would like to introduce to the readers is: “Seiten no heki-reki” For those of you moderately fluent in Japanese, the phrase is: “晴天の霹靂” The literal translation is “Thunderclap from a clear sky” or simply stated, “A complete surprise” or as Gomer Pyle USMC used to say; “Surprise, surprise, surprise.” Similar to our friends at FDA, the regulatory authorities in Japan do not like surprises.
Folks – over the years Dr. D has witnessed, on many occasions, the perception of corrective action being viewed as a negative experience. In fact, I have seen good quality people chastised for receiving a corrective action to mitigate necessary systemic issues. Viewing corrective action as a bad thing and punishing individuals or organizations for receiving a corrective action request (CAR) is a position diametrically opposite to the doctor’s view of a CAR being a proactive approach to fix problems. Repeat after Dr. D; “CARs are our friends.” No, the doctor has not lost his mind. When it comes to fixing QMS-related issues, it is never a good thing to “extemporize” (look-it-up) a solution when a permanent fix can be achieved through an effective approach to formal corrective action. That being said, this edition of DG is all about understanding the components of corrective action and how to ensure an organization’s approach to corrective action is in compliance with Article 63 of MO 169. Enjoy!
Ministerial Ordinance Number 169 (2004)
Chapter Two “Manufacturing Control and Quality Control in Manufacturing Sites of Medical Device Manufacturers, etc.”
Section Six – Measurement, Analysis, and Improvement
(Corrective Actions)
Article 63 The manufacturer, etc. shall take the corrective actions which are appropriate to the effects of the nonconformities encountered to eliminate the cause of the nonconformities in order to prevent the recurrence.
2. The manufacturer, etc. shall ensure that the documented procedure is established to define the following requirements.
(1) To review the nonconformities (including the customer complaints),
(2) To determine the causes of the nonconformities,
(3) To evaluate the need for the actions to ensure that the nonconformities do not recur,
(4) To determine and implement the actions needed, including, if appropriate, updating the documentation,
(5) To record the results of any investigation and of the actions taken , and
(6) To review the corrective actions taken and their effectiveness.
What device manufacturers need to know
Dr. D likes Article 63 because it is so simple and easy a caveman can open a CAR (thank you GEICO). Seriously, what can be easier than writing a corrective action procedure for an experienced quality/regulatory person? If you answered “absolutely everything” you would be correct. A corrective action procedure requires a significant amount of intelligent thought to ensure all aspects required of an effective corrective action process are captured. As a minimum, Article 63 requires the following salient elements to be formally addressed in a corrective action procedure. Dr. D suggest that one plans ahead and incorporates the preventive action requirements (Article 64) into the corrective action procedure; henceforth, creating a CAPA procedure.
- All non-conformances, including complaints, must be thoroughly reviewed for determination if they are corrective action worthy. Dr. D is pretty sure that most non-conformances identified are worthy of a CAR, especially complaints.
- Root-cause determination of a non-conformance is required. What a novel idea, understanding the underlying cause of a problem prior to attempting to fix it.
- An evaluation of potential actions needed to prevent a recurrence of a nonconformance is a fundamental requirement.
- Once appropriate action(s) have been determined, implementation of the identified action is required to occur.
- All corrective actions, including the investigative process, are required to be documented. Remember, if an event, action, or issue is not documented, it never happened. For you wise guys and gals out there, if a non-conformance is not documented, the non-conformance still happened; and failure to act will become problematic. Just ask PMDA.
- One final requirement for meeting Article 63; and the cornerstone of an effective approach to corrective action, is the verification of effectiveness (VOE) phase. Folks, it is all too often that Dr. D sees the VOE phase missing from the corrective action process; and routinely identified during the performance of one of the doctor’s QMS audits. VOE needs to be performed; otherwise, what is the point of pursuing corrective action?
What device manufacturers need to do
Since the pursuit of corrective action is a requirement of every QMS known to man, Dr. D will not pontificate about the need to establish a corrective action procedure and actually pursue corrective action, when appropriate. Instead, the doctor will give the readers some of the finer points associated with corrective action; and for the doctor’s experienced readers, re-enforce the points of an effective corrective action system.
For starters, not all problems will require formal corrective active, so some common sense is necessary during the initial review of a non-conformance. If the non-conformance is rooted in a customer complaint, there had better be a pretty darn-good reason for not pursuing corrective action. For everything else, use the CAR process. Having a CAR review, as an initial step in the corrective action, allows a device manufacturer to assess the non-conformance and determine if formal corrective action is warranted. If all CARs being opened are reviewed and closed with no formal corrective action being pursued, the QMS must truly be impeccable; or the corrective action system is broken. Chances are it is the latter, so Dr. D suggests breaking out plenty of swords for everyone to fall on.
Once a decision to move to corrective action has been made, there should be a corrective action form that captures key phases needed to be completed such as: (a) containment phase; (b) root-cause investigation phase; (c) corrective action plan phase; (d) implementation phase; (e) verification of effectiveness phase; and (f) closeout phase. The doctor is quite sure most device manufacturers have a functional corrective action system that is supported by a corrective action form. In fact, they probably are using pre-defined steps and/or phases. The corrective action system may even have a fancy name. That being said, the name of the doctor’s approach is: “Dr. D’s six-Phase Approach to Corrective Action.” Pretty catchy, eh?
- Containment Phase: If the corrective action is being driven by a product issue, containment becomes essential, especially if a RECALL (the doctor’s favorite 6-letter word) is pending. The containment phase should result in all product affected by the corrective action identified and quarantined. Of course with product already out of the immediate control of a device manufacturer, all bets are off. However, if the corrective action is related to a product safety and efficacy issue, the manufacturer better be talking to their customers and the regulatory authorities in Japan. Chances are probably pretty good that affected product is being sold in other markets as well (like the United States), so do not forget to give FDA a ring on the telephone.
- Root-Cause Investigation Phase: Make no mistake, if a sloppy approach is employed when performing the root-cause analysis and investigation, it will be a daunting task indeed attempting to identify and implement effective corrective action. If a medical device manufacturer is incapable of execution effective corrective action, after the Japanese regulatory folks finish having their way with them, their competitors will swoop down and grab market share, whenever possible. Dr. D strongly recommends using tools such as DMAIC and the 8 Disciplines of Problem Solving to support the investigative process. After all, Taguchi and Deming spent a lifetime creating tools that can be employed in support of root-cause analysis. The best advice the doctor can give is do not take short cuts.
- Corrective Action Plan Phase: Some corrective actions can be relatively simple with actions required to fix the nonconformance implemented immediately. However, in most cases, some level of planning will be required. For example, a piece of capital equipment may need to be replaced on the manufacturing floor so procurement activities and equipment validation activities (IQ, OQ, and PQ) will be required. These activities take time to complete. If the corrective action forces a product design change, a regulatory requirement for formal notification, review and approval by PMDA becomes a salient requirement. This takes time and requires a plan. Remember, a failure to properly plan is a plan for failure.
- Implementation Phase: Once the corrective action plan has been approved, the fun begins. The plan must be executed. If there are delays in implementation or adjustments to the plan are warranted, these changes must be documented and approved.
- VOE Phase: It is Dr. D’s opinion VOE is one of most important phases of corrective action. As stated earlier, if VOE is not performed, what is the point of corrective action? The fundamental question that needs to be asked is when does VOE get performed? The short answer is “it depends.” What kind of answer is that Dr. D? It depends! All kidding aside, if the corrective action is to change a calibration cycle on a piece of measuring equipment, due to a calibration failure or issue, then VOE would not occur until the next calibration interval has occurred. If the corrective action is much more succinct like changing the color of catheter handle from green to white, once the green handles are removed from inventory and the white ones placed into service, VOE can occur. One final example, if corrective action is as simple as adding an additional requirement for a signature on a form, once the document change order has been processed, VOE can occur. For everything else, a good rule of thumb is 90-days. If corrective action is deemed ineffective, it is back to the proverbial drawing board. Chances are pretty good the initial root-cause investigation was not adequate.
- Closeout Phase: The closeout phase occurs when all corrective action activities are successfully completed, period! Dr. D has seen some organizations play games with their metrics by closing corrective actions as ineffective and then opening new corrective actions. Rest assured, regulators frown down upon this approach. They do not like playing games.
For readers still mapping their QMS to MO 169, the doctor has populated this week’s requirements matrix (Table 1.0). Please note, Dr. D recommends combining corrective action and preventive action (next week’s discussion topic) into one procedure.
Procedure |
Procedure Name |
Requirement |
21 CFR, Part 820 |
EN ISO 13485:2003 |
MHLW MO 169 |
1272-1 Rev A |
Corrective & Preventive Action |
Corrective Action |
820.100 |
8.5.2 |
Article 63 |
Takeaways
For this week’s DG, the doctor will leave the readers with three very good pieces of advice. One – not all non-conformances will require formal corrective action. Use a CAR review process to make the decision to pursue formal corrective action. If the non-conformance is premised on a customer complaint, corrective action is probably warranted. Two – do not take short cuts during the root-cause investigation phase. If a poor job is executed in determining root cause, chances are the solution implemented will be ineffective. Three – always perform VOE. If VOE is ineffective it is back to the drawing board. It is time to revisit root-cause analysis.
Until the next edition of DG, when the doctor provides guidance on MO 169 – Chapter 2, Section 6 “Measurement, Analysis, and Improvement” (Article 64 – Preventive Action), sayonara from Dr. D and best wishes for continued professional success.
References:
- Code of Federal Regulation. (2011, April). Title 21 Part 820: Quality system regulation. Washington, D.C.: U. S. Government Printing Office.
- EN ISO 13485:2012. (2012, February). Medical devices – quality management systems – requirements for regulatory purposes (EN ISO 13485:2012).
- Linguanaut the Japanese phrases and expressions. (2012). Retrieved September 8, 2012, from http://www.linguanaut.com/english_japanese.htm
- Ministerial Ordinance 169. (2004). MHLW ministerial ordinance 169 on standards for manufacturing control and quality control for medical devices and in-vitro diagnostic reagents. Retrieved June 1, 2012, from http://www.pmda.go.jp/english/service/pdf/ministerial/050909betsu3.pdf
Also read:
Related Articles
-
Connected devices already enable remote patient monitoring by collecting real-time data, such as injection date and time. With time, these benefits are likely to grow. Following are three areas where manufacturers are exploring new uses of digitalization in drug delivery…
About The Author
Dr. Christopher Joseph Devine
President
Dr. Christopher Joseph Devine is the President of Devine Guidance International, a consulting firm specializing in providing solutions for regulatory compliance, quality, supplier management, and supply-chain issues facing the device industry. Dr. Devine has 32 years of experience in quality assurance, regulatory compliance and program management. He is a senior member of the American Society for Quality (ASQ), a member of the Regulatory Affairs Professionals Society (RAPS), and a member of the Project Management Institute, and resides on several technical advisory boards. Dr. Devine received his doctorate from Northcentral University, with his doctoral dissertation titled, “Exploring the Effectiveness of Defensive-Receiving Inspection for Medical Device Manufacturers: A Mixed-Method Study.” Dr. Devine holds a graduate degree in organizational management (MAOM) and an undergraduate degree in business management (BSBM).