MHLW MO 169 – Chapter 2/Section 6 – Control of Nonconforming Product

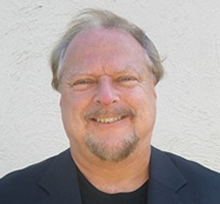
Ohayou Gozaimasu. This week the term/phrase specific to Japan, the doctor would like to introduce to the readers is: “
Saikin dou desuka?” For those of you moderately fluent in Japanese, the phrase is “
最近どうですか?”
The literal translation is “what’s new” If this question is coming from the good folks at PMDA, and your response is the entire Quality Management System (QMS), well – you just might have some explaining to do.
Dr. D would like to kick off this edition of Devine Guidance by stating emphatically, “Make no-mistake, the control of nonconforming product is one of the fundamental requirements of an effective QMS.” Organizations that fail to control their nonconforming product will soon be tasked with dealing problems associated with the doctor’s favorite dirty six-letter word RECALL! Other than shipping product, not approved for entry into the Japanese market, there is no faster exit strategy (forced the doctor might add) then shipping medical devices into Japan that are not safe and effective. In the eyes of the Japanese regulatory authorities, it makes no difference if the nonconforming product is procured materials, manufactured sub-assemblies, or finished medical devices. Nonconforming product is nonconforming product, is nonconforming product, is nonconforming product; and the doctor hopes each of the readers are catching Dr. D’s drift. Trust the doctor when I say, “Medical device manufacturers never want to be on the receiving of written correspondence from PMDA or MHLW that “excoriates” (look-it-up) their ability, or lack of, to manufacture finished medical devices that are safe and effective.
Ministerial Ordinance Number 169 (2004)
Chapter Two “Manufacturing Control and Quality Control in Manufacturing Sites of Medical Device Manufacturers, etc.”
Section Six – Measurement, Analysis, and Improvement
(Control of Nonconforming Products)
Article 60 The manufacturer, etc. shall ensure that the products which do not conform to the product requirements (hereinafter referred to as “nonconforming products”) are identified and controlled to prevent their unintended use or delivery.
2. The manufacturer, etc. shall ensure that the controls and related responsibilities and authorities for dealing with the nonconforming products are defined in the documented procedure.
3. The manufacturer, etc. shall deal with the nonconforming products by one or more of the following ways.
(1) To take actions to eliminate the detected nonconformity,
(2) To authorize their use, release or acceptance under the concession, or
(3) To take actions to preclude their original intended use or application.
4. The manufacturer, etc. shall ensure that the nonconforming products are accepted by the concession only if the regulatory requirements are met.
5. The manufacturer, etc. shall ensure that the records of the identity of the personnel authorizing the concession are maintained.
6. The manufacturer, etc. shall ensure that the records of the nature of the nonconformities and any subsequent actions taken, including the concessions obtained, are maintained.
7. The manufacturer, etc. shall ensure, when the nonconforming products are corrected, that they are subject to re-verification to demonstrate the conformity to the requirements.
8. When the nonconforming products are detected after the delivery or use has started, the manufacturer, etc. shall take actions appropriate to the effects, or potential effects, of the nonconformity.
9. If the products need to be reworked (one or more times), the manufacturer, etc. shall document the rework process in the work instructions that has undergone the same authorization and approval procedure as the original work instructions.
10. The manufacturer, etc. shall ensure that, prior to the authorization and approval of the work instructions, a determination of any adverse effect of the rework upon the products is made and documented.
What device manufacturers need to know
The entire premise for Article 60 is based on one simple little concept, device manufacturers must control nonconforming product to prevent its unintended use. Additionally, effective controls must be put into place that allows for the identification, segregation, disposition, rework, and use of nonconforming material. Yes, the doctor mentioned use. I know some of the readers work for device manufacturers that make a habit out of granting concessions. Can you say use-as-is? Dr. D likes to dissuade my clients from relying on the mighty UAI because UAI of nonconforming product implies a design change. If the UAI is a fundamental necessity, please ensure your engineering folks and regulatory affairs folks review and approves the disposition. Make sure signatures are collected for all of the individuals authorizing the UAI disposition. Why? Because ceremonial swords will be made available to fall on if the decision results in a serious injury or death to the patient or user in Japan.
Additionally, ensure the procedure your organization writes to define the handling of nonconforming product clearly defines levels of authority for the review and approval of dispositions associated with nonconforming product. Considering, device manufacturers are paying good money for product that is compliant, feel free to return it to the vendor, a.k.a., RTV (accompanied by a supplier corrective action if it the material fails to meet requirements). After all, the best way to preclude further non-conformances is to ensure the supplier is well aware of the problem. I know it sounds harsh, but Dr. D believes that having poor suppliers eat the cost of a product return typically accelerates the learning curve.
A few other salient elements to consider during the scripting of an effective procedure for control of nonconforming product are:
- The retention of meticulous records;
- Verification/inspection of all rework performed;
- Expediting appropriate actions, with a sense of urgency, when it has been determined that nonconforming product has shipped (left the device manufacturer’s control); and
- Clear definition of the rework process and the identification of potential adverse effects of rework on the finished medical device.
What device manufacturers need to do
For starters, Dr. D strongly recommends scripting an SOP that clearly defines all aspects of the control of nonconforming product as it influencing your specific organization. For example, there is definitely more latitude in manufacturing a piece of capital equipment that is categorized as a low risk device for Japan (Class II) versus a coronary stent delivery system that is a Class IV, when attempting to rationalize a concession. By the way, just in case the readers haven’t figured it out yet, Dr. D hates concessions. Would you by a new car if there was a minor issue (dent in the door) that did not affect the car’s performance? Heck no! Then why would you ask a healthcare provider or physician to accept a less than perfect medical device?
Make sure the established procedure adequately addresses all aspects of Article 60, not just partial compliance. Yes, the doctor said partial compliance. Dr. D does not believe in partial compliance, minimum compliance, maximum compliance, or significant compliance. There is only compliance! That being said, the doctor strongly recommends that an adequate quarantine area be constructed to hold non-conforming product. If the quarantine area is a cage or fenced-off area, make sure it has a top/roof. Years ago in a far-off land called California; Dr. D was blessed with the experience of having a marketing guy climb over the fence and into the MRB area to retrieve a catheter. Within 24-hours, the cage has a roof. As for the offending individual, he may be still locked in that MRB cage. Dr. D lost the key! For those of you that are keeping up with the mapping of standards and regulations to your QMS, Table 1 contains this week’s map.
Procedure |
Procedure Name |
Requirement |
21 CFR, Part 820 |
EN ISO 13485:2003 |
MHLW MO 169 |
1269-1 Rev A
|
Control of Nonconforming Product |
Control of Nonconforming Product |
820.90 |
8.3 |
Article 60
|
Takeaways
For this week’s guidance, the doctor will leave the readers with just on takeaway. Granted, the control of nonconforming product should never be an onerous task. Keep it simple, by never allowing non-conforming product to make its way into your organization’s supply chain. Yes – UAI is convenient, but eventually the use of such concessions is going to break your heart.
Until the next edition of DG, when the doctor provides guidance on MO 169 – Chapter 2, Section 6 “Measurement, Analysis, and Improvement” (Article 61 – Analysis of Data), sayonara from Dr. D and best wishes for continued professional success.
- Code of Federal Regulation. (2011, April). Title 21 Part 820: Quality system regulation. Washington, D.C.: U. S. Government Printing Office.
- EN ISO 13485:2012. (2012, February). Medical devices – quality management systems – requirements for regulatory purposes (EN ISO 13485:2012).
- Linguanaut the Japanese phrases and expressions. (2012). Retrieved September 8, 2012, from http://www.linguanaut.com/english_japanese.htm.
- Ministerial Ordinance 169. (2004). MHLW ministerial ordinance 169 on standards for manufacturing control and quality control for medical devices and in-vitro diagnostic reagents. Retrieved June 1, 2012, from http://www.pmda.go.jp/english/service/pdf/ministerial/050909betsu3.pdf.
Related Articles
-
Connected devices already enable remote patient monitoring by collecting real-time data, such as injection date and time. With time, these benefits are likely to grow. Following are three areas where manufacturers are exploring new uses of digitalization in drug delivery…
-
Beginning October 1, 2023, the FDA’s Total Product Life Cycle Advisory Program (TAP) Pilot will expand to include the Office of Neurological and Physical Medicine Devices (OHT5).
-
The acquisition expands Veranex’s footprint for product design engineering services across the U.S., with combined company offices now in the Eastern, Central, and Western regions
-
The acquisition brings MAXIS’ expertise in pre-clinical engineering, design validation and verification, regulatory affairs, field clinical services, and trial management to Avania’s contract research and MedTech development capabilities.
About The Author
Dr. Christopher Joseph Devine
President
Dr. Christopher Joseph Devine is the President of Devine Guidance International, a consulting firm specializing in providing solutions for regulatory compliance, quality, supplier management, and supply-chain issues facing the device industry. Dr. Devine has 32 years of experience in quality assurance, regulatory compliance and program management. He is a senior member of the American Society for Quality (ASQ), a member of the Regulatory Affairs Professionals Society (RAPS), and a member of the Project Management Institute, and resides on several technical advisory boards. Dr. Devine received his doctorate from Northcentral University, with his doctoral dissertation titled, “Exploring the Effectiveness of Defensive-Receiving Inspection for Medical Device Manufacturers: A Mixed-Method Study.” Dr. Devine holds a graduate degree in organizational management (MAOM) and an undergraduate degree in business management (BSBM).