MHLW MO 169 – Chapter 2/Section 5 – Control of Monitoring & Measuring Devices

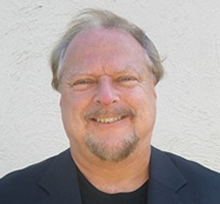
Ohayou Gozaimasu. This week the term/phrase specific to Japan, the doctor would like to introduce to the readers, is “
Watashi to issho ni kite kudasai.” The literal translation, come with me. Now if the individual speaking this phrase is also handing you a ceremonial sword, you may want to consider quickly walking in the other direction, as you may be asked to fall on it. On a serious note, the control of measuring and monitoring equipment is a fundamental requirement for all quality management systems (QMS) and multiple regulatory environments.
The bottom line in regards to compliance with Ministerial Ordinance 169 (MO 169) is quite simple folks. Equipment employed for the monitoring, measuring, testing, and/or inspection of medical devices must be properly maintained and calibrated. Dr. D will let you in on a little secret; this requirement applies to your suppliers as well. Few things are more frustrating than having a supplier provide non-conforming product only to find out that the supplier has no clue in regards to basic metrology concepts. Even worse, a supplier does not see the value in calibrating their tools because of the added expense; and develops a lame approach to calibration in an attempt to rationalize their poor judgment. If you want to see the doctor’s “Mercurial” (look-it-up) temperament swing from pleasant to just plain nasty, have an organization’s failure to calibrate their measuring equipment result in a product recall for one of my clients. As John Fogerty, of CCR fame, would say; “I see a bad moon rising.”
Ministerial Ordinance Number 169 (2004)
Chapter Two “Manufacturing Control and Quality Control in Manufacturing Sites of Medical Device Manufacturers, etc.”
Section Five – Product Realization
(Control of Monitoring and Measuring Devices)
Article 53 The manufacturer, etc. shall determine the monitoring and measurement to be undertaken and the monitoring and measuring devices needed to provide the evidence of the conformity of the products to the determined requirements.
2. The manufacturer, etc. shall establish the documented procedure to ensure that the monitoring and measurement specified in preceding Paragraph 1 can be carried out and are carried out in a manner that is consistent with the monitoring and measurement requirements.
3. Where necessary to ensure valid results, the manufacturer, etc. shall ensure that the measuring equipment meets the following requirements.
- To be calibrated or verified at the specified intervals, or prior to the use, against the measurement standards traceable to the measurement standards (in case where no such standards exist, the basis used for the calibration or verification shall be recorded),
- To be adjusted or re-adjusted as necessary,
- To be identified to enable the calibration status to be determined,
- To be safeguarded from the adjustments that would invalidate the measurement result, and
- To be protected from damage and deterioration during the handling, maintenance and storage.
4. The manufacturer, etc. shall assess and record the validity of the previous measuring results when the equipment is found not to conform to the requirements.
5. The manufacturer, etc., in case where they correspond to the case specified in preceding Paragraph 4, shall take appropriate action on the equipment and for any of the products affected.
6. The manufacturer, etc. shall ensure that the records of the results of the calibration and verification are maintained.
7. The manufacturer, etc. shall ensure that, when used in the monitoring and measurement of the specified requirements, the ability of the computer software to satisfy the intended application is confirmed prior to the initial use and reconfirmed as necessary.
What device manufacturers need to know
In accordance with Article 53 of MO 169, device manufacturers must take a little initiative and determine their requirements needed for ensuring the monitoring and measuring devices selected are adequate. For example, if a feature on a critical component is specified at 0.005” +/- .001, a micrometer better be the measurement tool of choice versus a caliper. Additionally, similar to all of the other MO 169 requirements, the device manufacturer must script a procedure that clearly delineates, with extreme granularity the doctor might add, the structure of their calibration program. You see, it is not enough to define the selection process and use the correct piece of equipment for monitoring and measuring. The equipment must actually be calibrated prior to its use. Wow, using calibrated equipment to measure stuff, who knew Dr. D?
As a minimum, MO 169 requires the calibration procedure to contain/delineate:
- Reasonable calibration intervals (hopefully to the manufacturer’s standard);
- The requirement to actually calibrate equipment using standards traceable to a recognized national standard (e.g., NIST in the United States);
- Depict equipment adjustment and readjustment requirements, when deemed appropriate;
- Equipment to be labeled in a manner to quickly ascertain the calibration status (e.g., a Cal Sticker);
- Equipment to be safeguarded from someone making unauthorized adjustments that could invalidate measurement results;
- The Assessment of previous measurement results and the pursuit of appropriate action when equipment is found to be out of calibration or specification tolerances;
- Evaluation of the impact non-conforming measuring equipment has on finished medical devices;
- Maintenance and retention records of all calibration activity; and
- The verification and validation of software, when employed in support of measuring and monitoring activities.
What device manufacturers need to do
It is Dr. D’s humble opinion, the calibration of monitoring and measuring devices is one of the cornerstone procedures needed to support an effective QMS. It is also one of the areas where the doctor sees way too many suppliers taking shortcuts in an effort to save money. But hey, this is the medical device industry and calibrating measuring and monitoring equipment, despite the added expense, is part of the price for admission into this industry. If a supplier does not want to calibrate their tools, fine. They should turn in their ISO certificate and move to a non-regulated industry. Sorry for the venting folks, but the doctor has seen one too many recalls linked to supplier performance issues, including calibration (or lack of).
Not wanting to state the obvious but obliged to do so, it all starts with a robust procedure. Since the control of monitoring and measuring devices and the general concept of equipment calibration is fundamental requirement for most regulatory environments, you can start by mapping the various regulatory requirements to your calibration SOP (reference Table 1.0). To ensure compliance with MO 169, ensure all of the requirements are addressed within the calibration procedure. If your organization is fully compliant with EN ISO 13485:2012, then chances are you comply because the requirements are basically identical. Additionally, Dr. D strongly recommends selecting a qualified metrology service that is accredited to ISO/IEC 17025:2005. Organizations such as SIMCO Electronics (no Dr. D is not a paid spokesperson for this supplier) specialize in providing metrology services for the medical device industry.
Procedure |
Procedure Name |
Requirement |
21 CFR Part 820 |
EN ISO 13485:2003 |
MHLW MO 169 |
1264-1 Rev A |
Calibration of Inspection, Measuring, & Test Equipment |
Control of Measuring and Monitoring Devices |
820.72 |
7.6 |
Article 53
|
Takeaways
For this edition of DG, the doctor will leave the readers with just one takeaway. Make sure all of the monitoring and measuring devices employed in the manufacture of finished medical device are properly maintained and if used for inspection, testing, and acceptance activities, “calibrated!” Make sure the suppliers you use in support of obtaining conforming materials, used in the manufacture of finished medical devices, maintain and calibrate their equipment as well. In short, there is no acceptable excuse for not maintaining and calibrating equipment – including costs!
Until the next edition of DG, when the doctor provides guidance on MO 169 – Chapter 2, Section 6 “Measurement, Analysis, and Improvement” (Articles 54 and 55 – Measurement, Analysis, and Improvement and Feedback), sayonara from Dr. D and best wishes for continued professional success.
- Code of Federal Regulation. (2011, April). Title 21 Part 820: Quality system regulation. Washington, D.C.: U. S. Government Printing Office.
- EN ISO 13485:2012. (2012, February). Medical devices – quality management systems – requirements for regulatory purposes (EN ISO 13485:2012).
- Linguanaut the Japanese phrases and expressions. (2012). Retrieved September 8, 2012, from http://www.linguanaut.com/english_japanese.htm.
- Ministerial Ordinance 169. (2004). MHLW ministerial ordinance 169 on standards for manufacturing control and quality control for medical devices and in-vitro diagnostic reagents. Retrieved June 1, 2012, from http://www.pmda.go.jp/english/service/pdf/ministerial/050909betsu3.pdf.
Related Articles
-
Tonometry-derived features showed superior performance compared to other feature groups and baselines, while younger and normotensive subjects had the most consistent readings across all feature groups.
-
“The solution provider that builds the device and creates the algorithm should consider integration and accountability among multiple other challenges. But meeting the needs of the third element in the equation, the doctors, is key.”
-
Connected devices already enable remote patient monitoring by collecting real-time data, such as injection date and time. With time, these benefits are likely to grow. Following are three areas where manufacturers are exploring new uses of digitalization in drug delivery…
-
New data presented at the Technology and Heart Failure Therapeutics (THT) Conference showed that hemodynamic monitoring can slow the progression of heart failure in patients with reduced ejection fraction.
About The Author
Dr. Christopher Joseph Devine
President
Dr. Christopher Joseph Devine is the President of Devine Guidance International, a consulting firm specializing in providing solutions for regulatory compliance, quality, supplier management, and supply-chain issues facing the device industry. Dr. Devine has 32 years of experience in quality assurance, regulatory compliance and program management. He is a senior member of the American Society for Quality (ASQ), a member of the Regulatory Affairs Professionals Society (RAPS), and a member of the Project Management Institute, and resides on several technical advisory boards. Dr. Devine received his doctorate from Northcentral University, with his doctoral dissertation titled, “Exploring the Effectiveness of Defensive-Receiving Inspection for Medical Device Manufacturers: A Mixed-Method Study.” Dr. Devine holds a graduate degree in organizational management (MAOM) and an undergraduate degree in business management (BSBM).